There are several processes and secondary operations that are used to produce powder metal (PM) components, and one of those key processes in PM part production is heat treatment. Heat treating powder metallurgy parts is a necessary process to control the properties of the final part, such as hardness and strength. Although some properties associated with heat treating can be attained through sintering alone, there are additional heat treatment processes that are needed to give each component its desired properties, such as carburizing, hardening, and tempering, just to name a few.
Sintering is the process in which a green PM part is placed in a continuous belt furnace with a controlled atmosphere to bond the powder together and give the part strength. Before bonding can take place, there are two precursors that must be achieved during sintering: removal of the pressing lubricant through the oxidation and burning of the vapors, and reduction of the surface oxides from the powder particles in the compact. Without removing the lubricant and reducing the surface oxides, the final part would either be too brittle or lack strength.
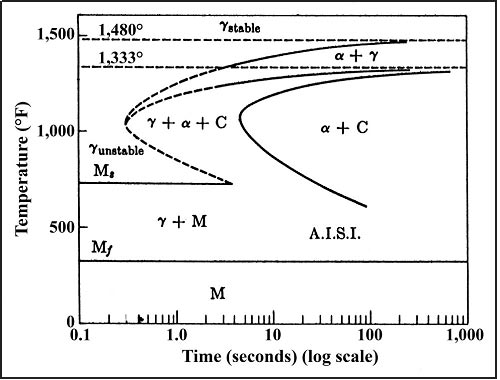
Figure 1. The image shows a time-temperature-transformation diagram for a 1040 steel.
To control the properties during sintering, PM parts fabricators have to control the temperature and atmosphere in sintering furnaces. A common furnace atmosphere is nitrogen (N2) and 10% hydrogen (H2), although a mixture of other gases can be added.1 For example, adding a small amount of methane (CH4) can help avoid decarburization. The carbon in methane combines with water vapor and latent oxygen in the atmosphere and forms CO or CO2, rather than combining with the carbon in the iron, which is necessary for good hardness.2
Once sintering is completed, additional heat treatment processes can be undertaken to help improve the overall properties of the PM parts and give them better properties specific to the parts’ function. PM components that require high wear resistance generally need a higher hardness. To gain higher hardness, the parts can go through a hardening process, and one of the parameters that can determine that process is hardenability.
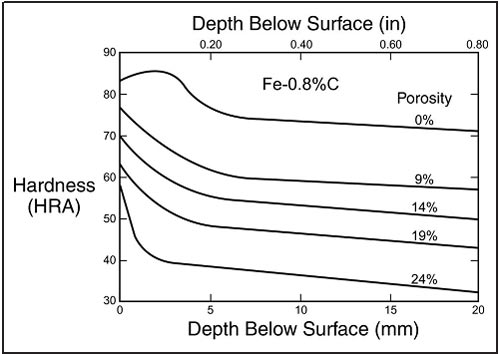
Figure 2. The relationship between porosity and depth of hardness. As porosity increases, hardness decreases.
Hardenability can be defined as the ease of hardening the material. One way this can be used is to characterize the ability to heat treat a thick part or section to a high hardness. For example, higher hardenability indicates that a slow cooling rate can be used to gain high hardness in a thick section of a part.3 Figure 1 shows a time-temperature-transformation (TTT) diagram for a 1040 (.4%C) steel.4 TTT diagrams are useful for determining the cooling rate necessary to obtain the desirable transformation in the final product. Desired phases for generating good strength and toughness are martensite and bainite which are both phases with high hardness. The TTT diagram in Figure 1 shows that if martensite were the desired phase, a very rapid cooling rate would be needed, usually through quenching.
Hardenability can also be affected by the porosity of the material, as pores reduce thermal conductivity and hinder the formation of the microstructures that would provide the final high strength.5 Figure 2 is a diagram showing the relationship between the depth of hardness and the porosity of the material.6
Figure 2 above shows the hardness versus depth for end- quenched cylindrical test bars of varying porosity, from 0% to 24%. The bars with lower porosity clearly maintained higher hardness at greater depths than those with higher porosity. Since PM components are inherently porous, this relationship is important for the hardening process of PM parts.
Alloy additions can also impact hardenability in PM components. A heat treatment method known as precipitation hardening relies on the relationship between solid solubility and temperature to create particles of an impurity phase that acts to impede the movement of dislocations or crystal defects, thus increasing the hardness of the material. Common alloy additions include nickel or copper, but many other alloying elements can be used. For example, a 2012 paper investigated mechanical properties of PM steels alloyed with silicon and vanadium.7
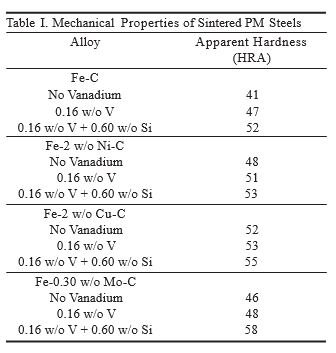
Table I shows the correlation between the alloying element, the amount added, and the apparent hardness of sintered PM steels. Copper as an alloying addition is known to promote the formation of pearlite and decrease ferrite, which increases hardness as a result. High levels of copper may saturate the ferrite in this alloy system, preventing additional alloying elements from increasing the hardness any further. Alloy additions and the heat treatment process are important in developing the physical and mechanical properties of PM components.
Hardening is just one of the qualities that can be achieved through heat treating a PM component, tempering is another option. Tempering is a post-quenching process that trans-forms or modifies the microstructure usually to improve toughness at the expense of hardness. The tempering process involves heating the part to a temperature below its critical point for a specific amount of time. The exact temperature at which the part is heated to will determine how much hardness is removed. Examples include austempering, which yields bainite in the microstructure, and martempering, which yields martensite.
The physical and mechanical properties of PM components are determined by many factors. The alloy used and the sintering process are each important to the final quality of the part, but heat treatment is a way to accurately control the final properties with a high degree of accuracy.
References
1. H. Ferguson, Heat Treatment of Ferrous Powder Metallurgy Parts, Powder Metal Technologies and Applications Handbook Desk Edition, Seventh Edition, ASM International, 1998, p. 651
2. Ibid., p. 652
3. L.F. Pease, III, W.G. West, “Heat Treating of Powder Metallurgy Parts,” Fundamentals of Powder Metallurgy, 2002, p. 203.
4. Ibid., p 202.
5. R.M. German, Powder Metallurgy & Particulate Materials Processing, 2005, p. 346
6. Ibid., p. 347
7. C.T. Schade, T.F. Murphy, A. Lawley, R. Doherty, “Microstructure and Mechanical Properties of PM Steels Alloyed With Silicon and Vanadium,” Inter. J. Powder. Metall., 2012, vol. 48, no. 6, p. 41-45.