With careful tool design, good process capabilities, and CNC closed-loop control of compaction, most machining of powder metallurgy (PM) components is potentially unnecessary. In many cases, the close tolerance of dies and close control of powder choices (control of part-size change due to material selection) means that what machining may be necessary due to application requirements can be quite manageable.

Figure 1. Fishbone diagram showing some of the parameters involved in PM machining characterization and troubleshooting
That being said, there are machined features, such as cross holes, undercuts, and threads, that cannot be formed into place due to PM's nature as a net-shape axial-compaction process. Use of machining charts produced for wrought materials will likely result in marginal results. Within the last decade, considerable effort has been expended by the PM industry to address this issue, starting with understanding PM’s microstructural relationship to machinability as well as machinability characterization, admixed and prealloyed additives, and technologies such as “green machining” (machining an un-sintered PM compacted component).1
Machining high-density PM parts (those >92% density) is similar to machining wrought materials.2
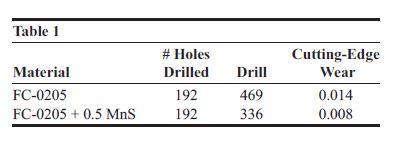
Figure 1 characterizes those variables that impact PM machining. Methodically addressing these variables one at a time will help optimize a machining practice for a given material. As with all metals, machining practice for a given material in a given "condition" will impact speeds, feeds, and cutting-tool choice.3
When considering PM machining, one of the key variables is the porosity (or density) of the component. Traditional approaches to improving machinability have been to infiltrate the component's pores with resin. This fills the pores and provides some lubrication, thus stopping the tools from over- heating and "chattering." Similarly, copper can be used to infiltrate the part with the added value of increasing part strength, but at an increased cost, however.4
As found in wrought machining, alloy additives such as manganese sulfide can enhance the machinability of an alloy. Table I compares a widely used iron–copper PM alloy with and without MnS.
The additive use of MnS resulted in 25% less drill force and 50% of the cutting tool wear.5
Figure 2. Effect of sulfur-containing additives on the drillability of FC-02086
Another approach to improving PM machining efficiency is to select a more-successful cutting-tool geometry. Switching from a conventional high-speed steel chisel point to a sculptured edge, three flute drills resulted in a nearly ten-fold increase in the number of holes drilled in non-leaded brass.7
Machining procedures for self-lubricating porous components should avoid closing surface porosity. Sharp tools and light cuts should be used in single-point machining to reduce shearing of the workpiece surface. A PM coating such as titanium nitride will reduce tool wear and cutting forces on either carbide or HSS tooling. Cooling fluids may or may not improve procedures.7
References
- C. Blais, “Machining of PM Materials: A Secondary Shaping Operation of Primary Concern”, Inter. J. Powder Metall., 2008, vol. 44, no. 2, pp. 13–14.
- Powder Metallurgy Design Manual, Third Edition, 1998, Metal Powder Industries Federation, Princeton, NJ, pp. 119–120.
- D. Christopherson, “Characterization of PM Machinability: Practical Approach and Analysis”, Inter. J. Powder Metall., 2008, vol. 44, no. 2, pp. 15–20.
- L.F. Pease, III, and W.G. West, Fundamentals of Powder Metallurgy, 2002, Metal Powder Industries Federation, Princeton, NJ, pp. 183–185.
- ibid., p. 185.
- B. Lindsley, “Machining of PM Steels: Effect of Additions and Sinter Hardening”, Inter. J. Powder Metall., 2008, vol. 44, no. 2, p. 25.
- Powder Metallurgy Design Manual, Third Edition, 1998, Metal Powder Industries Federation, Princeton, NJ, p. 120.