Powder metallurgy (PM), as a manufacturing process, encompasses numerous forming, treating, and finishing operations. In many, but not all cases, the PM process transforms the powder into components used for structural applications, for example, gears, bearings, connecting rods, and parts used in medical instruments. There are also times when powders are needed in powder form, as in the electronics industry, or for components that are not structural in nature, such as sound insulation.
Any element from the periodic table that can be found at room temperature and above in a solid form can be produced as a powder by chemical, mechanical, or pyrometallurgical means. In powder form, any elemental or alloyed material can be mixed into any chemical combination.
The selection of materials available for PM processing covers a very extensive range of materials. A complete enumeration is too lengthy for the present discussion, but an illustrative listing of materials in typical components made from metal powder is provided below.
- Iron/steel
- Stainless steel
- Copper
- Aluminum
- Tin
- Magnesium
- Titanium
- Tungsten/tungsten carbide
- Molybdenum
- Precious metals (e.g., gold, silver, platinum)
The majority of PM-based materials found in industrial use include combinations of iron and other metallic, semi-metallic, or transitional elements. The powders typically are mixed by combining pure elemental powders, or are prealloyed so that each particle has the same chemistry. It is not possible to compact steel powder; therefore, the ability to mix elemental powders, specifically iron and graphite, makes it possible to compact steel components. Additionally, tungsten powder can be mixed with cobalt or other elements in order to “bond” the particles. It would be difficult, if not impossible, to process tungsten via any other method due to its high melting temperature.
Design
Function and consumer requirements affect the choice of material properties such as strength, ductility, and wear resistance. Manufacturing processes can also affect material properties.1 Given the infinite variability of mixed powders, a truly wide range of property alternatives such as machinability, formability, and weldability can be designed into the metal powder used for mechanical components.
Alloying Examples
Figure 1. Ultimate tensile strength and yield strength as a function of copper content
Copper powder is recognized for its ability to strengthen and harden ferrite (an iron–carbon mixture of specific chemical range). Moderate amounts (<0.20 w/o) are used in wrought steels to provide resistance to atmospheric corrosion. However, higher copper content in wrought materials causes segregation in molten steels.2 In PM materials, 1 w/o copper will increase yield strength by 70–140 MPa, regardless of the effects of other alloying elements. Bear in mind, however, that there may be diminishing returns, as shown in Figure 1.2
Nickel and molybdenum offer similar performance characteristics. Molybdenum additions have a robust effect on hardenability (the ability to form the iron phase martensite). Nickel is known to increase toughness when added between 2 and 4 w/o.3
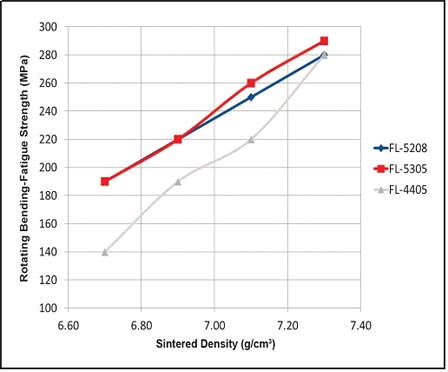
Figure 2. Rotating-bending-fatigue strength; conventional sintering
Chromium-containing alloys exhibit exceptional fatigue properties compared with other prealloyed PM alloy systems, as shown in Figure 2.4 Chromium and manganese exhibit a high hardening effect on steels.5
Microalloying (percent addition <0.05–0.20 w/o) can be used to refine grain size and thus improve mechanical properties. Niobium and vanadium affect this by limiting austenite-grain growth via the formation of precipitates, yielding significant improvement in strength and ductility.6
Similarly, many ceramic materials are processed via a powder manufacturing route. Combining ceramic and metals enables us to obtain composites and functionally graded materials with unique microstructures unobtainable by any other means.
Powder metallurgy offers a world of materials to the engineer, designer, artist, crafter, and more generally the public, for a multitude of uses.
References
- Metals Handbook–Desk Edition, 2nd edition, 1998, ASM International, Materials Park, OH, p. 122.
- E. Ilia, G. Lanni, C. Thompson, and K.T. Tutton, “Another Look at the Effect of Copper on the Mechanical Properties of As-Sintered Iron–Copper–Carbon Alloys”, Intl. J. of Powder Metall., 2013, vol. 49, no. 3, pp. 35–42.
- P. Sokolowski, B. Lindsley, and K. McQuiag, “Designing Lean Heat- Treatable Alloys for the PM Industry”, Intl. J. of Powder Metall., 2013, vol. 49, no. 2, pp. 52–54.
- R.T. Warzel III and S.H. Luk, “Effect of Processing Conditions on the Fatigue Response of PM Chromium Steels”, Intl. J. of Powder Metall., 2012, vol. 48, no. 5, pp. 19–22.
- M. Selecká and A. Šalak, “Industrial Sintering of Hybrid Low- Carbon 3Cr-0.5 Mo-xMn Steels”, Intl. J. of Powder Metall., 2010, vol. 46, no. 4, pp. 29–42.
- C. Schade, T. Murphy, A. Lawley and R. Doherty, “Microstructure and Mechanical Properties of Microalloyed PM Steels”, Intl. J. of Powder Metall., 2012, vol. 48, no. 3, pp. 51–59.